Maintaining precise temperature control in cold storage facilities is crucial for operational excellence across various industries. Whether it’s pharmaceutical storage or food processing, the quality of temperature-sensitive products relies on effective monitoring systems.
Temperature monitoring devices act as vigilant guardians in cold chain management, offering:
- Real-time temperature tracking to prevent product degradation
- Automated documentation for regulatory compliance
- Early warning systems to protect valuable inventory
- Data-driven insights for operational optimisation
The stakes are particularly high in cold storage environments, where even minor temperature fluctuations can result in significant product losses. Modern temperature monitoring solutions combine advanced sensor technology with sophisticated software platforms to create comprehensive surveillance systems.
These monitoring systems serve a dual purpose of ensuring both product quality and regulatory compliance. They establish an unbroken chain of documentation while allowing quick responses to any temperature excursions that could jeopardise stored materials.
Understanding Different Types of Temperature Monitoring Devices
Cold storage facilities rely on various monitoring devices to maintain precise temperature control. Each device serves specific functions and offers unique advantages for different operational needs.
1. Temperature Sensors
- High accuracy within specific temperature ranges
- Limited by fixed installation points
There are several types of temperature sensors used in cold storage:
- Resistance Temperature Detectors (RTDs): These sensors measure temperature by correlating the resistance of the RTD element with temperature. They are known for their accuracy and stability over a wide temperature range.
- Thermocouples: Thermocouples consist of two different metals joined at one end. They generate a voltage that is proportional to the temperature difference between the junction and the other end. Thermocouples are versatile and can measure extreme temperatures.
- Thermistors: These are temperature-sensitive resistors that exhibit a significant change in resistance with temperature. Thermistors are commonly used for precise temperature measurements in limited ranges.
2. Data Loggers
- Cost-effective solution for small operations
- Requires manual data collection
Data loggers are standalone units with internal memory that record temperature readings over time. They are battery-powered and often equipped with USB connectivity for easy data retrieval. Data loggers offer a cost-effective solution for small cold storage operations where manual data collection is feasible.
3. Wireless Sensors
- Flexible installation options
- Higher initial investment costs
Wireless sensors provide real-time monitoring capabilities by transmitting temperature data wirelessly to a central system or cloud platform. This eliminates the need for physical connections and allows for flexible installation in hard-to-reach areas. However, wireless sensors may require a higher initial investment compared to wired alternatives.
4. Temperature Alarms
- Essential for critical storage areas
- Dependent on power supply
Temperature alarms are crucial for maintaining the integrity of sensitive products stored in cold facilities. These systems trigger immediate alerts through audio-visual notifications when predefined temperature thresholds are breached. Programmable threshold settings allow for customised alarm parameters based on specific requirements.
5. Circular Chart Recorders
- Traditional regulatory compliance
- Limited data analysis capabilities
Circular chart recorders are mechanical devices that continuously document temperature on a rotating paper chart. While they provide physical records of temperature history, they have limitations in terms of data analysis capabilities compared to digital solutions.
The selection of appropriate monitoring devices depends on specific facility requirements, storage conditions, and regulatory standards. Modern cold storage operations often implement multiple device types to create comprehensive monitoring systems that ensure product safety and quality control.
Key Features to Consider When Choosing Temperature Monitoring Devices
Real-time Alerts
Real-time alerts serve as critical safeguards against temperature excursions, enabling immediate response to prevent product loss. These alerts can be customised to trigger at specific temperature thresholds, sending instant notifications when conditions deviate from acceptable ranges.
Remote Monitoring Capabilities
Remote monitoring capabilities allow staff to track cold storage conditions from any location, providing:
- Continuous visibility of temperature data
- Instant access to historical records
- Ability to respond to issues outside business hours
- Reduced need for manual temperature checks
Cloud-based Systems
Cloud-based systems offer enhanced data security and accessibility through:
- Automated data backup
- Secure storage of temperature records
- Multi-user access with permission controls
- Integration with existing business systems
Audit Trail Requirements
Regulatory compliance demands comprehensive documentation of temperature monitoring activities. Modern systems maintain detailed audit trails recording:
- Temperature readings
- Alert acknowledgements
- Corrective actions taken
- System modifications
- User access logs
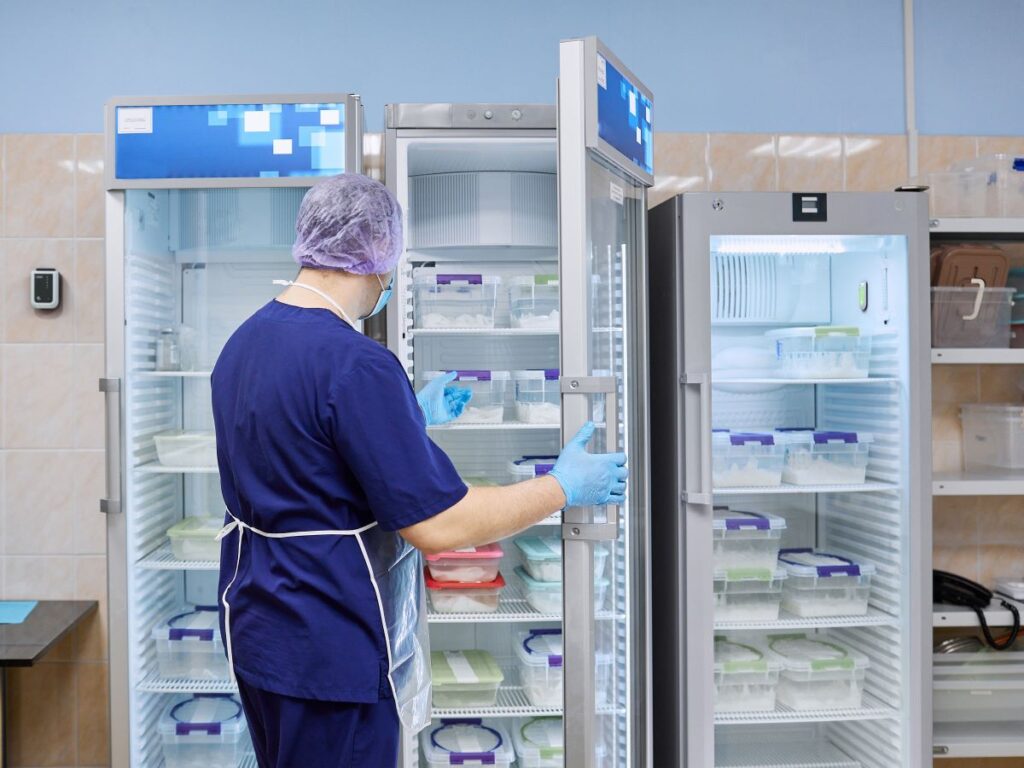
Scalability Features
Large-scale operations require monitoring systems that can grow with business needs:
- Easy addition of new monitoring points
- Multi-site data aggregation
- Centralised management capabilities
- Flexible reporting options
The right combination of these features creates a robust monitoring system capable of protecting temperature-sensitive inventory while meeting regulatory requirements.
Environmental and Operational Considerations in Cold Storage Temperature Monitoring
Cold storage environments demand precise temperature monitoring devices capable of withstanding extreme conditions while maintaining accuracy. Different storage applications require specific temperature ranges:
- Ultra-Low Temperature Storage (-80°C): Specialised sensors with enhanced calibration and durability features
- Standard Freezer Range (-20°C): Robust devices with frost-resistant components
- Refrigeration (2°C to 8°C): Standard temperature monitoring equipment
Monitoring Methods:
- Continuous Monitoring: Records data 24/7, provides comprehensive temperature history, enables trend analysis, ideal for critical storage requirements
- Spot Checks: Manual temperature readings at set intervals, suitable for less critical applications, requires staff intervention, limited historical data
Device Durability Requirements:
- Waterproof or water-resistant construction
- Impact-resistant housing
- Anti-condensation features
- Frost-resistant components
- Extended battery life in cold conditions
The harsh conditions of cold storage environments necessitate devices built with industrial-grade materials. Stainless steel probes, reinforced cables, and sealed enclosures protect against moisture, frost, and physical damage. Temperature monitoring devices must maintain accuracy despite temperature fluctuations, high humidity levels, and frequent door openings.
Integration and Automation Capabilities of Temperature Monitoring Systems
Modern temperature monitoring systems offer sophisticated integration and automation features that are changing the way we manage cold storage. These systems connect seamlessly with multi-channel alert notifications, enabling instant response to temperature changes.
Alert System Integration
- SMS text alerts for immediate notification
- Automated phone calls to designated personnel
- Email notifications with detailed temperature logs
- Push notifications through mobile applications
- Customisable alert thresholds for different storage zones
Automated record-keeping eliminates manual data entry errors and creates comprehensive audit trails. Digital systems capture temperature readings at preset intervals, generating accurate timestamps and maintaining detailed histories of storage conditions.
Automated Record-Keeping Benefits
- Elimination of paper-based documentation
- Reduction in human error
- Time savings through automated data collection
- Enhanced accuracy in compliance reporting
- Simplified audit preparation
Secure SaaS platforms serve as centralised hubs for temperature monitoring data. These cloud-based solutions provide:
- Real-time monitoring through internet-connected devices
- Secure data storage with encryption
- Multi-user access with permission controls
- Historical data analysis capabilities
- Remote system management options
Advanced integration capabilities allow temperature monitoring systems to communicate with existing building management systems, creating a unified approach to facility oversight. These interconnected systems enable automated responses to temperature excursions, such as activating backup cooling systems or adjusting ventilation controls. Additionally, leveraging insights from Azure Monitor can further enhance the effectiveness of these systems by providing advanced analytics and monitoring capabilities.
Industry Applications and Compliance Requirements for Cold Storage Temperature Monitoring Devices
Temperature monitoring devices serve distinct roles across various industries, each with specific regulatory demands and operational requirements.
Food Manufacturing and Processing
- HACCP compliance mandates precise temperature control throughout production
- Documentation of cold storage conditions for raw ingredients and finished products
- Regular temperature verification during transportation and distribution
- Automated alerts for deviations from safe temperature zones
Pharmaceutical Cold Chain Management
- Strict adherence to GDP (Good Distribution Practice) guidelines
- Temperature-sensitive vaccine storage between 2°C and 8°C
- Specialised monitoring for ultra-cold storage requirements (-80°C)
- Uninterrupted temperature logging for batch quality assurance
Industry-Specific Standards
- FDA 21 CFR Part 11 compliance for electronic records
- ISO 22000 requirements for food safety management systems
- WHO guidelines for pharmaceutical storage and distribution
- Regular calibration and validation of monitoring devices
The implementation of reliable monitoring solutions helps organisations maintain product integrity while meeting stringent regulatory requirements. These systems provide detailed audit trails, demonstrating compliance during inspections and supporting quality assurance programmes. Advanced monitoring solutions adapt to specific industry needs, offering customised reporting templates and alert thresholds aligned with regulatory frameworks. Check out more about remote temperature monitoring system setup for multi-site kitchens.
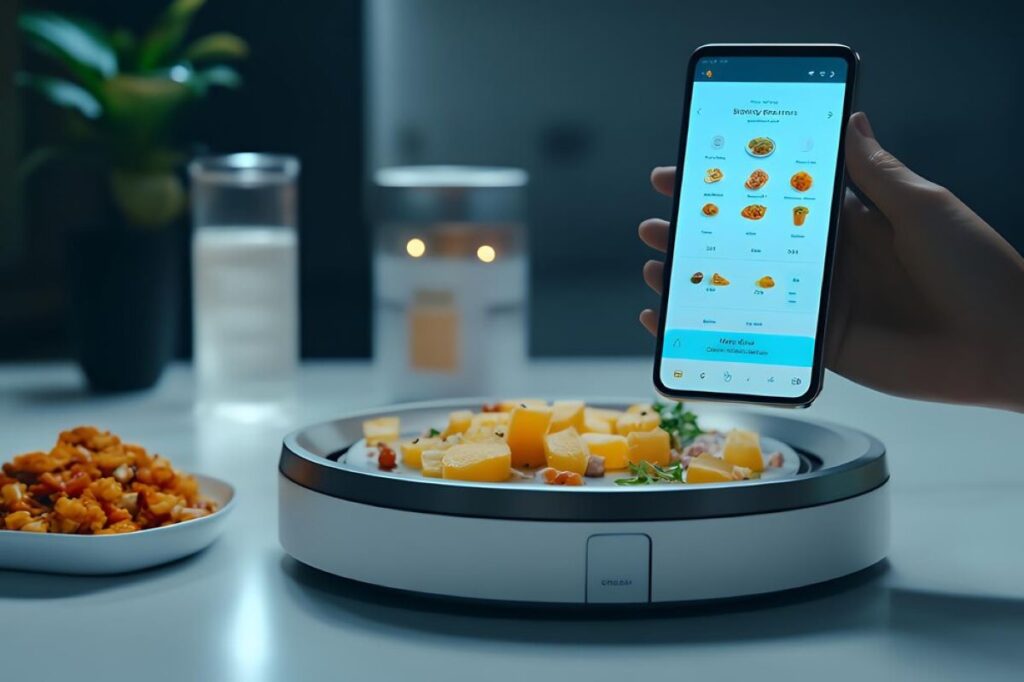
Selecting a Reliable Partner for Cold Storage Temperature Monitoring System Implementation
Successful temperature monitoring implementation relies heavily on choosing the right system partner. A reliable partner should offer:
- Customised Solutions
- Tailor-made checklists adapted to specific operational needs
- Configurable software parameters
- Flexible integration options with existing systems
- Comprehensive Onboarding Support
- Detailed system demonstrations
- Discovery calls to understand unique requirements
- Step-by-step implementation guidance
- Staff training programmes
The ideal partner provides robust technical capabilities through a secure SaaS platform, ensuring:
- Real-time data accessibility
- Automated record-keeping functions
- Multi-device compatibility
- Regular system updates
24/7 Support Availability
A dedicated support team should possess deep compliance expertise across various industries, helping organisations:
- Navigate regulatory requirements
- Maintain audit-ready documentation
- Implement best practices
- Address compliance gaps
The right partner acts as an extension of the organisation’s quality control team, providing ongoing guidance and support to maintain optimal cold storage operations.
Conclusion
Investing in advanced temperature monitoring systems is crucial for cold storage operations in various industries. By strategically implementing these technologies, businesses can significantly improve product safety, meet regulatory requirements, and increase operational efficiency.
Successful cold storage monitoring relies on:
- Selecting devices that meet specific temperature needs
- Implementing comprehensive monitoring solutions with real-time alerts
- Choosing systems that enable automated documentation
- Partnering with providers offering customised support
The right temperature monitoring solution makes cold storage management easier and more efficient. With modern systems that have remote monitoring capabilities and automated record-keeping, businesses can consistently maintain optimal storage conditions.
Upgrading temperature monitoring infrastructure is an essential step towards improving operations. To ensure better cold storage safety and compliance, it is important to select monitoring devices that align with the unique needs of the business and industry standards.